What is a work order? Which departments play an active role in work order management processes?
We can define a work order as a process that is widely used by manufacturing businesses.
If we need to talk about it in a little more detail, it includes the tasks assigned to the personnel working in production, including the routes and product recipes of the sub-operations. For example, each line in the factory may be producing a different product or each operator may be working to produce a different product. A work order, on the other hand, provides precise information such as which line or which operator should produce what at that moment and how many units should be produced.
In the second question, the planning department manages the work orders, but it should not do this alone but together with the production site.
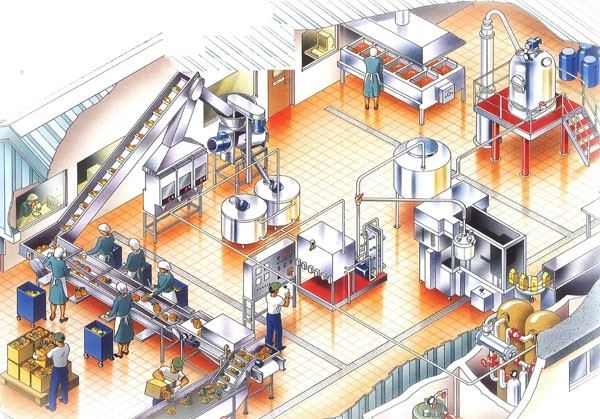
As you can see from the image, there may not be only one department or one workbench in an enterprise. Work order management actually puts an end to the chaos in enterprises, synchronizes the units and takes control from the beginning to the end of production. As we can see here, if the work order of the operator working at the control point is created for the operator carrying the case, production will stop because the operator does not know what to do, and the main purpose of the work order, which is the fast, high quality and uninterrupted completion of production, will be interrupted.
What are the difficulties of managing work orders in the classical way, i.e. on paper?
When creating a work order, it is very important to look at the history for that work order (approval-starting-completion-closing-plans-actualizations) etc. It is important to see.
The follow-up of work orders opened in paper environment may be disrupted during or after production. There are declaration inaccuracies and the frequency of writing, i.e. sampling, will be insufficient. Filtering the production parameters of the same or similar work orders will take time, require a lot of effort or, as in the majority, will not be possible.
For example, a company that wants to make a new investment in a press line should decide whether to make a progressive prestream or tandem prestream for a work order by looking at the data of previous work orders. It may be desirable to examine the work order history on an equipment-specific basis. Capacity utilization and determining the most suitable production route for that product cannot be done in paper tracking or the degree of difficulty is high. It may be desired to examine work order history on personnel basis. Similar situation applies. The file related to the work can be stored, for example, the most frequent error visuals for the product to be worked on will be requested to download the work order with technical drawing dwg. All sub-operations that will work on the work order or those selected may want to look back at this technical drawing at any time of production. A mixture will be created in the kitchen according to the work order created recipe. Whether this mixture has the right ingredients and weight can be done autonomously with an electronic scale instead of a paper checklist.
What are the planned maintenance plans of the equipment and machine park, and what is the impact of this maintenance on work order management should be measured. For example, when a critical equipment such as a mold will undergo scheduled maintenance, mold change time or waiting time should be predictable. The data needed in every situation similar to these cannot be sustainable in a paper environment.
What is the contribution of ERP and MES Systems integration to work order management?
Businesses manage their processes such as production planning, supply chain, human resources, customer relations, financial management with ERP systems that they are familiar with, but there is another section that ERP systems cannot reach, which is the Production Area. MES, i.e. Manufacturing Execution Systems, builds this bridge with the integration method.
ERP-MES Integrations can be done on the most basic basis; transferring stock information and work orders from ERP to MES System and transferring production confirmations from MES to ERP. In addition to these, quality control, maintenance, personnel, LOT tracking, document management and similar processes depending on field needs can be integrated.
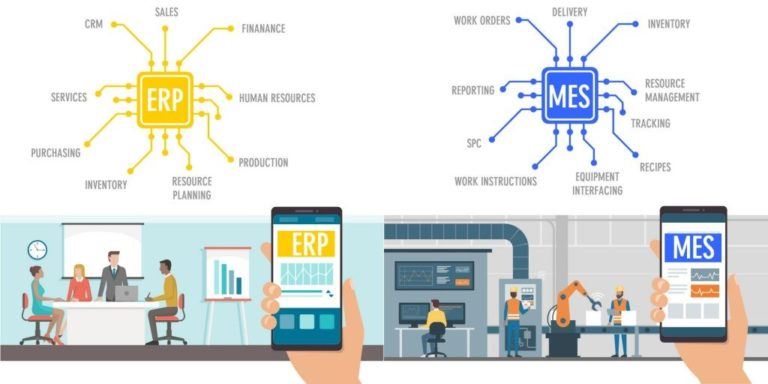
In the integration process, standard procedures are applied and work is carried out together with the stakeholders in this process depending on the specific requests and needs of the organization. After the work order transfer from the ERP system to the MES System, processes such as opening the plan suitable for this work order and transferring it to the stations suitable for their operations are carried out within the MES System.
In summary; The inclusion of the production area in this system, such as managing many departments together in ERP, both prevents human error in production data and reduces the processing load. The fact that the work order opened through ERP falls directly in front of the operator at the machine and that the operator can access the details and guides related to this production is very important in terms of workload, time and quality-accurate work. In work order management, dynamic data such as what the ideal route is in your machine pool in the same specifications of your machine park and similar dynamic data can be collected from the field with MES and brought to the ERP layer. It can also enable work order planning according to capacity utilization.
What should be considered when creating work order plans?
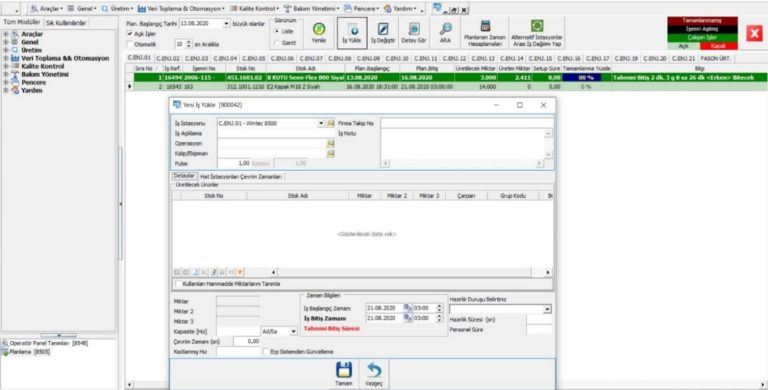
As can be seen in the image above, it is necessary to know and analyze the production site very well before creating a work order. Just as creating a work order allows us to keep many situations under control, it will also ask us to provide precise information about the product to be produced. Information such as which station to work at, which equipment to use, how much production will be made, between which dates this work will be done, should be analyzed in advance and a work order should be created accordingly.
.png)
First of all, the main reason for creating a wrong work order is that the production site is not sufficiently known and analyzed well. For example, if a press machine that can press 200 tons is loaded with a job that needs to press 300 tons, the work done by the planning department will be wasted, the machine and the operator will wait idle because production cannot be achieved, and even in a worse scenario, if that product is accidentally tried to be produced there, the materials used will be scrapped or even the machine will break down and serious losses will occur. However, if an effective work order management is made and the units work in synchronization, if it is known what should be produced on which machine, the main purpose of fast, high quality and uninterrupted production will emerge.
What are the benefits of the Gantt chart for work order management?
The Gantt chart provides a visual representation of the scheduled work in a given time interval. As can be seen from the program image below, it is not only a visual, but also a screen where you can manage work orders such as distributing work orders by dragging by observing the machine distribution, job splitting due to intervening jobs for certain reasons, closing a certain time interval due to planned maintenance.
The biggest benefit of the Gantt chart in work order management is that it allows the assignments to be made to the machine to be made accordingly, since it can be clearly seen how long the planned jobs will take over the cycle time and quantity, it can be prevented from assigning work to the time that is closed for a certain reason with an error, in summary, the workload distribution can be done in an optimum way.
In line with the demands and researches we receive in our report designs, we know that visuals are always more understandable than numbers and texts and can tell much more at a glance. With this feature, the Gantt chart stands out compared to many work order management tools.
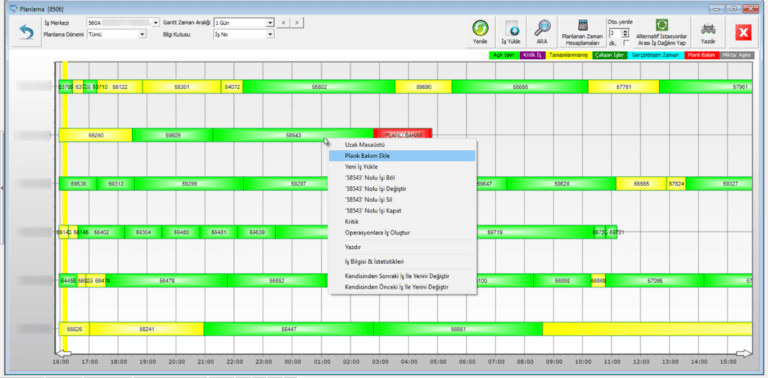
What is required for effective work order management? What are the benefits of effective work order management?
- It requires being dynamic. In order to be dynamic, it is necessary to be able to access the right data, detailed data easily and quickly.
- It is necessary to be able to trace backwards. It is necessary to determine the man/hour planning and machine utilization time required for the mentioned work order.
- It is important to be able to instantly see what will be encountered from the set-up histories made in that work order, to see where planned maintenance can be extended or where it can be withdrawn.
- It is important to see the quality values in the history of that work order.
- Flexibility is necessary. Temporary changes may need to be made to the outlined workflow format for non-standard or short deadline orders.
- It needs to be understandable. In large organizations with a planning team, it should be easily understandable and manageable why this job is on this line or why it is in this work order sequence, it should not be left to the planner's workplace experience, it should be managed in a way that every planning staff can easily understand and adapt.
Saves Time, Effort, Energy, Raw Materials.
To what extent does the sector or process make a difference in work order management and how are customizations carried out in the program in this direction?
To illustrate with an example; in a line production business (e.g. filling industry), the machines are connected and dependent on each other by conveyors. In such a business, since the final product that can be sold can be obtained after the last process and due to the series of processes applied to a linearly available product, a line-based work order will be needed here instead of talking about a separate work order for each machine. Again in this context, since the equipment of the line works at a synchronous speed, the planned speed value in the work order created on a line basis in ERP can be calculated in the MES System in line with the number of products output by the equipment and thus a real performance calculation can be made.
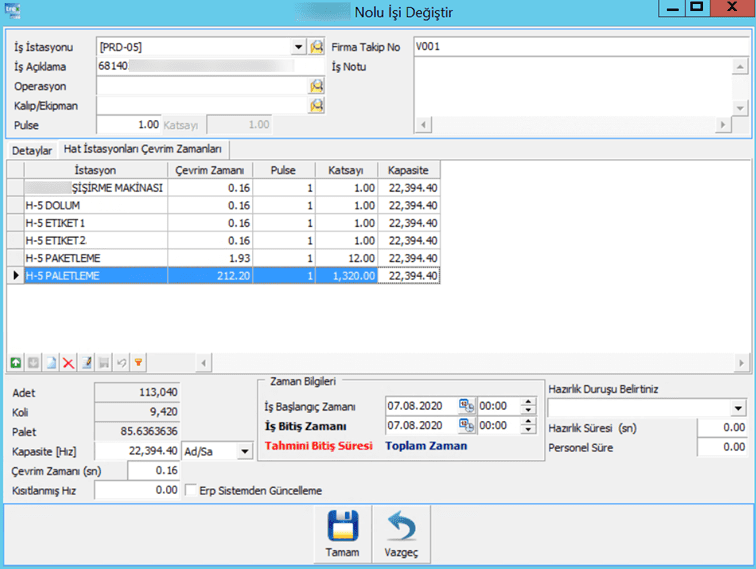
For example, this image is a planning screen detail image and shows the equipment of the line. Depending on the product type, a filled bottle may be packaged in 12 packs as shown here and may be packaged in 1320 pieces in the same way. In this case, the packaging operation speed (1.93 sec) can be obtained by multiplying by 12 over the production time of 1 product, and the packaging operation speed (212 sec) can be obtained by multiplying by 1320, and the MES System already performs this automatically. This is actually a sectoral work order management customization in the program.
In line production systems, there may be a long period of time between the start of the first operation and the same product reaching the last operation. In such cases, the first operation may have started the next job B even before job A is finished. Therefore, it is correct that the first machine in the line should be able to display all the jobs to be worked on. However, it is sufficient for other equipment to see only the jobs loaded by the first equipment. This will prevent the selection of the wrong job. In the aforementioned example, it is logical to switch to job B after job A is worked, but if job C is started while job A is still loaded in the line, in this case, the MES System also supports the use of poka-yoke, such as warning on the panels that the wrong job is being worked. Such examples can be multiplied on a sector-process basis.
Another example; In ERP systems that track raw material consumption, for example in the automotive sector, the stock information to be consumed in the work order created automatically falls on the panel and the consumed raw material LOT data can be automatically transferred from the panel to the ERP System. At the same time, the material consumption used in faulty productions can be seen and analyzed.
If we look at all these from a general point of view, it has become a necessity of the new age to provide retrospective traceability free of extra workloads and to automatically transfer information from office to field, from field to office.
What is the role of MES Systems in ideal work order management?
- Planning is the first and most important step in the production process. It will give the road map.
- Even if it is the right production practice, the wrong plan does not give good results. The right plan and the right production practice bring success together.
- The ideal work order management is to maximize the machine and equipment capacity and the performance of the existing personnel and to produce high quality production in the shortest time possible.
- Good, but how to answer the questions of how, when and who. They will be answered if there is information or as much information as there is.
- Preparing shift, daily and weekly plans with paper, that is, the classical method, can take very long hours and sometimes days.
- What is needed in each operation, what is the setup time, what can be done in cycle times, what is the quality value, is there a bottleneck in the next operation, if so, what is the effect on this operation, etc. It takes a very long time to plan all these.
- When the work order plan is downloaded to the field, there are big differences between the planned and actual productions, revisions and updates to the plan, and ultimately a process that cannot be implemented.
- If the plan is created with the data to be fed by MES from the production site; the difficulty of planning dynamic, manageable, flexible work orders with paper, that is, with classical methods, is avoided.
- At every stage of production, MES plays a very active role as it is the first step of production in planning. It enables accurate, ideal planning.