Günümüzde endüstriyel işletmeler, verimliliği artırmak ve rekabet avantajı sağlamak amacıyla üretim süreçlerini sürekli olarak optimize etme gereksinimi duymaktadır. Bu çerçevede, Üretim Yürütme Sistemleri (MES) kritik bir öneme sahiptir. MES, üretim süreçlerinin gerçek zamanlı izlenmesi ve yönetilmesini sağlayarak verimlilik artışı ve maliyetlerin düşürülmesi gibi önemli avantajlar sunmaktadır. Bu sistemlerin temel bileşenlerinden biri olan çevrim zaman analizi, üretim süreçlerinin performansını doğrudan etkileyen önemli bir unsurdur.
Üretim süreçlerinde çevrim süresi, bir ürünün bir işlem için ne sıklıkta tamamlandığını gösteren en önemli verilerden biridir. Ancak, çevrim süresi hesaplamasında, metodoloji veya gerçek değerler açısından sıklıkla hatalar yapılır. Çevrim süresi, bir ünitenin başlangıcından bir sonraki ünitenin başlangıcına kadar geçen süre olarak hesaplanabilir ve makine çevrim süresi ile operatör çevrim süresine ayrılabilir.
1. Çevrim Süresi
Çevrim süresi, bir işlemi veya görevi başlangıcından sonuna kadar tamamlamak için geçen süreyi ifade etmektedir. İşletmeler için çevrim süresi, verimliliği artırmak, müşteri memnuniyetini artırmak ve maliyetleri en aza indirmek açısından kritik öneme sahiptir. Çevrim süresi iki ana bileşenden oluşur: makine süresi ve operatör süresi. Bu iki süre bazen tam çevrim süresinden daha uzun olabilmektedir.
Çevrim süresinin hesaplanması için formül:
Çevrim Süresi = Toplam Süre / Ürün Sayısı
Çevrim süresi, üretim sürecinin verimliliğini ve etkinliğini değerlendirmek için üretim yönetiminde önemli bir metriktir. Daha düşük bir çevrim süresi, daha verimli ve rekabetçi bir üretim sürecini göstermektedir. Çevrim süresi, akıllı fabrika uygulamaları ve insansız fabrika otomasyonu kullanılarak, 7/24 üretim olanağı sağlanarak azaltılabilmektedir.
Çeşitli üretim süreçleri için çevrim süresi hesaplamaları şu şekildedir:
Plastik enjeksiyon kalıplama: Çevrim süresi = Kapak kapanma süresi + Plastik enjekte etme süresi + Soğuma süresi + Kapak açılma süresi
Sac metal bükme makineleri: Çevrim süresi (s) = (Metal kalınlığı (mm) / Bıçak kalınlığı (mm)) * (1 / Bıçak hızı (mm/s))
Enjeksiyon kalıplama: Çevrim süresi (s) = (Hazırlık süresi (s) + Erime süresi (s) + Basma süresi (s) + Soğuma süresi (s))
Frezeleme makineleri: Çevrim süresi (s) = (Hazırlık süresi (s) + İşleme süresi (s))
Montaj hatları: Çevrim süresi (s) = (En uzun montaj süresi (s) / Hattaki parça sayısı)
1.1 Çevrim Süresi Ölçüm Yöntemleri
Çevrim süresi analizleri için en yaygın yöntem, belirli bir zaman diliminde kronometreyle doğrudan ölçüm yapmaktır. Ancak bu yöntemin gözlemci etkisi ve sınırlı zaman penceresi gibi riskler taşıdığı belirtilmektedir.
Üretim Yürütme Sistemleri (MES), ekipman verilerini otomatik olarak izleyebilir ve çevrim süresini sürekli kaydedebilir, böylece otomatik çevrim süresi analizi yapılabilir. Bu, manuel kronometreyle ölçüme kıyasla daha doğru ve kapsamlı veriler sağlar.
Çevrim zamanının hesaplanması için temel adımlar:
- Operasyonların Tanımlanması: İlk olarak, hangi operasyonların çevrim zamanına dahil edileceği tanımlanmalıdır. Bu operasyonlar, bir iş parçasının ham maddeden nihai ürüne dönüşümü sırasında gerçekleştirilen her türlü işlemleri kapsayabilir.
- Zaman Ölçümü: Her bir operasyon için gerekli olan zaman ölçülür. Zaman ölçümü, stoper, zaman kaydedici gibi araçlarla ya da daha teknolojik yöntemlerle, örneğin sensörler aracılığıyla otomatik zaman takip sistemleriyle yapılabilir.
- Bekleme ve Gecikmeler: İş parçasının bir operasyondan diğerine geçişi sırasında ortaya çıkan bekleme ve gecikme süreleri de hesaba katılır. Bu süreler, ekipman arızası, malzeme eksikliği veya iş akışındaki dengesizlikler gibi çeşitli nedenlerden kaynaklanabilir.
- Toplam Çevrim Zamanının Hesaplanması: Her operasyonun zamanı ve bekleme/gecikme süreleri toplanarak toplam çevrim zamanı hesaplanır.
- Toplam Cevrim Zamanı=∑(Her Operasyonun Zamanı + Bekleme ve Geçime Süreleri)
- Analiz ve İyileştirme: Toplam çevrim zamanı hesaplandıktan sonra, sürecin her aşamasında iyileştirme fırsatları araştırılır. En uzun süren veya en çok gecikmeye neden olan operasyonlar belirlenerek, bu operasyonların verimliliğini artırmak için stratejiler geliştirilir.
1.2 Çevrim Süresi Analizi
Çevrim süresi analizinin temel amacı, alt bileşenlerini inceleyerek üretim sürecini optimize etmektir. Bu bileşenler arasında etkin makine çevrim süresi, makine çevrim süresi ve operatör çevrim süresi yer alır.
Çevrim süresi analizi aşağıdaki alanlarda kritik öneme sahiptir:
Hat Dengeleme: Çevrim sürelerinin doğru analizi, hat dengeleme çalışmalarına yardımcı olur ve üretim hattının daha verimli hale getirilmesini sağlar.
SMED (Tek Dakikada Kalıp Değişimi): Çevrim süresi verileri, kalıp değişim sürelerinin iyileştirilmesi için kullanılabilir. Bu da daha kısa kurulum süreleri ve artan üretkenlik anlamına gelir.
Verimlilik Artışı: MES sistemleri, çevrim süresi analizleri sayesinde verimliliği artırır ve maliyetleri düşürür.
OEE Ölçümü: Çevrim süresi verileri, Toplam Ekipman Etkinliği (OEE) ölçümlerinde kullanılır.
Kalite Kontrolü: Kalite sorunlarının tespit edilmesine ve önlenmesine yardımcı olur.
Zaman Yönetimi: MES sistemleri, çevrim süresi analizleri ile zaman yönetimini iyileştirir.
Envanter Yönetimi: Doğru çevrim süresi verileri, envanter seviyelerinin optimize edilmesine olanak tanır.
Süreç Yönetimi: Çevrim süresi analizleri, süreçlerin iyileştirilmesine ve standartlaştırılmasına katkıda bulunur.
Setup Sürelerinin İyileştirilmesi
Kurulum sürelerinin iyileştirilmesi, üretim verimliliğini artırmak için kritik öneme sahiptir. MES sistemleri, kurulum sürelerini izlemek ve optimize etmek için çevrim süresi verilerini kullanır:
SMED (Tek Dakikada Kalıp Değişimi): SMED, kalıp değişim sürelerini azaltmak için sistematik bir yaklaşımdır. MES verileri, SMED uygulamalarını desteklemek için kullanılabilir:
• İç ve dış kurulum faaliyetlerini ayırarak
• Dış kurulum faaliyetlerini optimize ederek
• İç kurulum faaliyetlerini basitleştirerek
Otomatik Kurulum: Bazı MES sistemleri, kurulum süreçlerini otomatikleştirmeye yardımcı olur. Bu, insan hatalarını azaltır ve tutarlı kurulum sürelerini sağlar .
Kurulum Prosedürlerinin Standartlaştırılması: MES, çevrim süresi verilerini kullanarak kurulum prosedürlerini standartlaştırabilir. Bu, operatör eğitimini kolaylaştırır ve kurulum sürelerindeki değişkenliği azaltır.
Makine Kurulum Durumlarının İzlenmesi: MES, makine durumlarını ve kurulum adımlarını izleyebilir. Bu, sorunların hızlı bir şekilde tespit edilmesine ve giderilmesine olanak tanır.
Önleyici Bakım: Düzenli bakım, makine arızalarını ve beklenmedik duruşları azaltarak kurulum sürelerini iyileştirir. MES, önleyici bakım programlarını destekleyebilir.
Kurulum süreleri iyileştirildiğinde, üretim verimliliği ve ekipman kullanılabilirliği artar. Daha kısa kurulum süreleri, daha fazla üretim zamanı ve daha düşük maliyetler anlamına gelmektedir.
1.3 OEE VE ÇEVRİM SÜRESİ İLİŞKİSİ
OEE (Toplam Ekipman Etkinliği), üretim birimlerinin üretim sürecindeki performansı ve kayıpları ölçmek için kullandığı önemli bir KPI'dır (Anahtar Performans Göstergesi) . OEE, aşağıdaki üç ana parametreye bağlıdır:
- Kullanılabilirlik
- Performans
- Kalite
OEE = Kullanılabilirlik x Performans x Kalite
Çevrim süresi, OEE'nin Performans bileşenini etkileyen önemli bir faktördür. Çevrim süresindeki iyileştirmeler, Performans bileşenini ve dolayısıyla genel OEE değerini artırabilir .
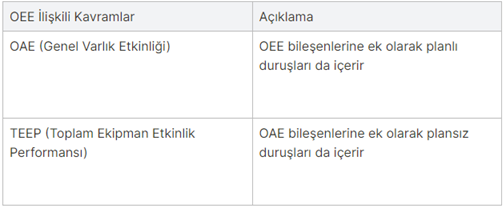
Üretim verilerini doğru bir şekilde takip etmek, OEE'yi hesaplamak için çok önemlidir. Bu veriler şunları içerir :
- Tarih
- Üretim siparişi
- Üretilen parçalar
- Başlangıç ve bitiş saatleri
- Operatörler
- Makine kodları
- İyi parçalar
- Hurda
- Yeniden işleme
- Arızalar
- Kurulum süresi
- Bekleme süresi
Bu metriklerin analizi, en büyük kayıpları belirleyerek iyileştirme (Kaizen) çabalarına odaklanmaya yardımcı olur . Yüksek OEE seviyeleri (%85 ve üzeri) "Dünya Sınıfı Üretim" olarak kabul edilir ve birçok şirket için bir hedef olmakla birlikte, kurulum süresi, küçük durmaları ve kalite gibi alanlarda önemli iyileştirmeler gerektirir.
MES'in dört ana işlevi
- Üretim zemininden gerçek zamanlı veri toplamak
- Verileri merkezi bir veri tabanında depolamak ve organize etmek
- Diğer sistemlerden kritik verilere erişim sağlamak
- ERP'den iş emirleri almak ve bunları üretim birimlerine dağıtmak
olarak ele alınmaktadır.
MES'in faydaları arasında üretim döngü süresini azaltmak, kurulum/tedarik süresini kısaltmak, ürün kalitesini artırmak, planlama sürecini geliştirmek ve fabrika işçilerinin verimliliğini artırmak da yer alır.
2.1 MES Sistemlerinin Teknik Yetenekleri
MES sistemleri, gerçek zamanlı veri toplama, analiz etme ve raporlama kapasitesi ile üretim sürecini bütünsel olarak yönetir. Bu sistemler, üretim hatlarında gerçekleşen işlem adımlarının izlenmesini, süreç kontrolünün sağlanmasını ve üretim performansının arttırılmasını mümkün kılar. Manufacturing Execution Systems , (MES) teknolojisi, endüstriyel üretimin verimliliğini ve esnekliğini artırma amacı güden bir bilgi sistemi olarak tanımlanır. Bu sistemler, fabrika katındaki operasyonları doğrudan kontrol ederek, planlama ve üretim süreçlerini etkili bir şekilde yönetir. MES, üretim verilerini gerçek zamanlı olarak toplar, analiz eder ve görselleştirir, böylece süreç optimizasyonu ve karar destek mekanizmaları için güncel ve doğru veri sağlar.
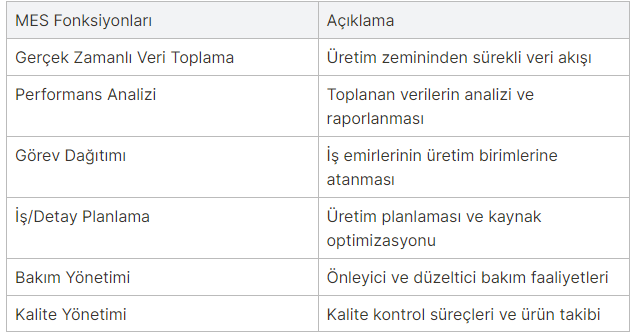
MES sistemleri, performans, kalite, kullanılabilirlik, bakım ve izlenebilirlik gibi geniş bir yelpazede üretim verilerini kaydedebilir. Bu sistemler, yapılandırılmış, yarı yapılandırılmış ve yapılandırılmamış verileri üretim zemininden toplayarak büyük veri işleme yeteneklerine sahiptir.
MES sistemleri, otomatik raporlama, eğilim analizi ve otomatik darboğaz tespiti, tahmine dayalı bakım gibi yapay zeka destekli uygulamalar da dahil olmak üzere gelişmiş raporlama ve analiz yetenekleri sunar. Bu sistemler, Endüstri 4.0'ın temel bir bileşeni olup, siber-fiziksel sistemler, Nesnelerin İnterneti, bulut bilişim ve yapay zeka/bilişsel bilişim ile entegre olarak daha kapsamlı, entegre ve otomatikleştirilmiş üretim süreçlerini mümkün kılar.
2.2 İyileştirme Yaklaşımları
MES sistemlerindeki özelleştirmelerin temel amaçları, şirketlerin MES sistemlerine daha hızlı uyum sağlamalarına yardımcı olmak ve üretim zemininden veri toplamak için en önemli kişiler olan operatörlerin programı kabul etmelerini kolaylaştırmaktır. Özelleştirmeler, MES sistemi ile fabrikadaki mevcut üretim kültürü arasındaki boşluğu kapatmada önemli bir rol oynar. Amaç, fabrika kültürünü bozmadan ve çalışanlara fazladan iş yükü getirmeden değişiklikler yapmaktır.
Özelleştirmeler hem sektörel ihtiyaçlardan hem de şirkete özgü talepler nedeniyle yapılabilir. Sektörel ihtiyaçlar genellikle müşteri talepleri doğrultusunda özelleştirmeleri şekillendirir, ancak aynı sektör içinde bile şirketler kullanıcı arayüzü, raporlama ve diğer sistemlerle entegrasyon gibi alanlarda farklı taleplere sahip olabilir. Özelleştirmelerdeki temel zorluklar arasında yeterli bütçe ayrılmaması, kilit personelin ayrılmasıyla kurumsal bilgi kaybı ve şirketlerin mevcut MES yeteneklerini tam olarak kullanamaması yer alır.
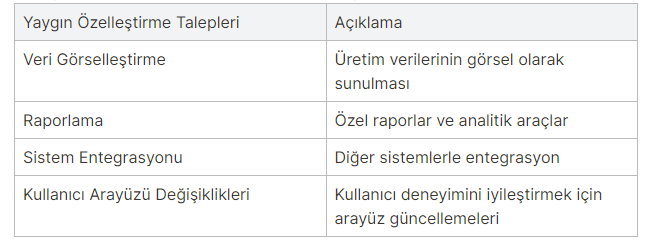
MES sağlayıcıları, özelleştirmeleri etkili bir şekilde gerçekleştirebilmek için güçlü sektör uzmanlığına, yetenekli proje ekiplerine ve donanım geliştirme yeteneklerine sahip olmalıdır. Özelleştirme çözümleri arasında çevrimiçi izleme, diğer sistemlerle entegrasyon ve kapsamlı kullanıcı tanımlı konfigürasyonlara izin veren esnek ANDON yönetimi özellikleri yer alır.
Özelleştirmelerin sürdürülebilirliğini sağlamak için uygun dokümantasyon ve sürüm kontrolü kritik öneme sahiptir. Güçlü sektörel deneyime sahip MES ortakları, müşterilerinin operasyonlarına en iyi uygulamaları ve sürekli iyileştirmeyi getirerek önemli değer sağlayabilir.
Özetlemek gerekirse, MES , (Üretim Yürütme Sistemleri), gerçek zamanlı veri toplama, analiz ve raporlama yetenekleriyle üretim süreçlerini optimize etmek için güçlü bir araçtır. Çevrim süresi analizleri, hat dengeleme, SMED, kurulum sürelerini iyileştirme, OEE ölçümü ve iyileştirme fırsatlarını belirleme gibi alanlarda kritik bir rol oynar. Doğru çevrim süresi verilerinin elde edilmesi, verimliliği ve etkinliği artırarak maliyetleri düşürür.